All electronic devices, and especially power amplifiers, inherently dissipate the electric power in order to operate. Since they have to deliver a considerable power to their load (hence the name), amplifiers need to draw a considerable power from the supply, resulting in the dissipation of power into heat.
Heat sinks are used to deal with the excess heat produced. A heat sink is a metallic part used to transfer heat from a device, like amplifiers, in order to prevent the device from overheating. Heat is transferred by conduction from the device to the heat sink, then transferred by convection from the heat sink to the surrounding air. Heat sinks increase the contact surface area between the device and the surrounding air, thereby increasing the opportunity to dissipate heat.
In this article we will discuss the mechanics of heat dissipation and how a thermal managements system known as ODEP is an innovative solution to the problem.
Heat Dissipation
A heat sink is important for the continuous operation of a power amplifier, as an improper thermal dissipation design can shorten the amplifier life or even damage it permanently.
The heat is generated at the heart of the output transistors’ chip, in what is called the die, which is the junction area of the actual semiconductor materials. The heat generated at the die is transferred directly to the metal case of the transistors; then from case to heat sink; then from heat sink to the atmosphere.
Figure 1 shows an “exploded view” of an output transistor device on a heat sink. It also shows the electrical equivalent to both steady-state (DC Model) and dynamic (AC Model) conditions.
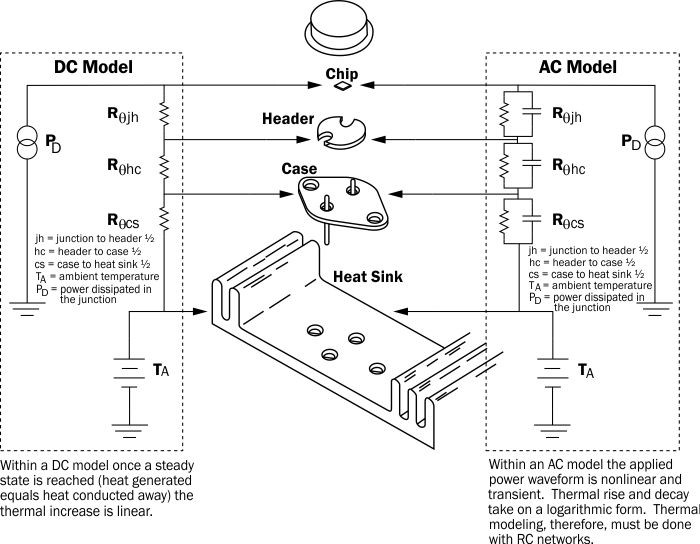
Figure 1: Heat Sink Simulations
Heat vs. Time
An amplifier’s power rating is typically based on its maximum continuous output. If the transistor sees a continuous waveform, it would eventually reach a steady state condition where the thermal sensor on the heat sink would see a temperature representing the actual transistor temperature. But often the waveforms to be amplified or the load the amplifier is driving is not constant, causing instantaneous heating conditions in the amplifier that a traditional sensor cannot respond to.
Once a heat sink is warmed up, the transistor cannot handle as much power because its ambient condition is already close to its thermal limits. This reduction in power handling capability per degree rise in temperature is called thermal derating. In this situation, the thermal switch cannot effectively respond to dangerous thermal conditions.
Most other manufacturers use a thermal sensor mounted on the heat sinks for thermal protection. When the heat sink gets hot enough, the sensor causes amplifier shutdown. The effect to the end user is potentially catastrophic – complete loss of amplifier output.
As described above, the basic thermal switch is also less effective as a means of protection. That is why AE Techron amplifiers use the innovative system known as ODEP.
ODEP Concept
ODEP stands for Output Device Emulation Protection and is a thermal management system which safely allows an amplifier to produce more power than an one with conventional VI limiting.
The most critical components in a power amplifier are the transistors in the output stage that drive the high voltage and current to the load. ODEP is a form of protection that ensures long term safe operation of these key transistors. As we have already stated, in a power amplifier the output stage is the major source of heat inside the chassis, and heat is the real concern during operation.
Essentially, ODEP is an analog computer which calculates the temperature at the die of the transistor. It senses output voltage and current, combining these to calculate output power. Heat sink temperature is also monitored. Temperature information is factored in for determining the amount of thermal de-rating.
Analog circuits measure the rate of change of temperature. Power and thermal information are used to build a model of the heat transfer process, store of history of operation, and ultimately determine the actual temperature at the die of the devices.
If the ODEP circuitry determines that the test signal is about to cause a dangerous thermal condition in the amplifier, it will limit the amplifier output enough to prevent damage. ODEP does not shut down the amplifier, although if conditions are extremely severe it can almost completely limit the amplifier output to prevent damage. With ODEP, the amplifier is protected at all times.
Crown International (AE Techron’s former parent company) holds the patent on ODEP, and AE Techron is the only industrial amplifier manufacturer to use this type of circuitry to calculate real thermal conditions.
Leave a Reply